0
0
У вас есть мобильник?
… точнее вы можете назвать хоть одного человека, который им не пользуется?
Пожалуй, на это вам хватит пальцев одной руки, потому что сотовая связь не просто влилась в нашу жизнь, а стала ее неотъемлемой частью.
Преимущества натяжных потолков это-время, ведь прямоугольное полотно с гарпунной системой, 10-15 кв метров возможно установить за 3-4 часа.
Для привлечения в свою фирму клиентов и увеличения прибыли просверлите дыры в трех мускатных орехах и нанижите их на зеленую нить, концы которой соедините вместе тройным узлом.
Как создать положительную энергетику для защиты родного дома? Тайные силы родного дома
Три правила для хозяек
1.
Остается загадкой - почему в представлении многих людей образ невесты устойчиво ассоциируется с принцессой или королевой? Казалось бы, монархия как форма правления давно изжила себя, и сегодняшние коронованные особы если и правят в какой-то стране, то чисто формально, чтобы отдать дань традициям, не более.
Правила половой жизни
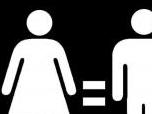
При лазерной резке нагревание и разрушение участка материала осуществляется с помощью лазерного луча.
Общепринятые обозначения
LBC – Laser Beam Cutting – резка лазерным лучом
Сущность процесса
В отличие от обычного светового луча для лазерного луча характерны такие свойства как направленность, монохроматичность и когерентность.
За счет направленности энергия лазерного луча концентрируется на относительно небольшом участке. Так, по своей направленности лазерный луч в тысячи раз превышает луч прожектора.
Лазерный луч по сравнению с обычным светом является монохроматичным, т. е. обладает фиксированной длиной волны и частотой. Это облегчает его фокусировку оптическими линзами.
Лазерный луч имеет высокую степень когерентности – согласованного протекания во времени нескольких волновых процессов. Когерентные колебания вызывают резонанс, усиливающий мощность излучения.
Благодаря перечисленным свойствам лазерный луч может быть сфокусирован на очень маленькую поверхность материала и создать на ней плотность энергии, достаточную для нагревания и разрушения материала (например, порядка 108 Вт/см2 для плавления металла).
лазерная резка металла
Технология лазерной резки металла
Воздействие лазерного излучения на металл при разрезании характеризуется общими положениями, связанными с поглощением и отражением излучения, распространением поглощенной энергии по объему материала за счет теплопроводности и др., а также рядом специфических особенностей.
В области воздействия лазерного луча металл нагревается до первой температуры разрушения – плавления. С дальнейшим поглощением излучения происходит расплавление металла, и фазовая граница плавления перемещается в глубь материала. В то же время энергетическое воздействие лазерного луча приводит к дальнейшему увеличению температуры, достигающей второй температуры разрушения – кипения, при которой металл начинает активно испаряться.
Таким образом, возможны два механизма лазерной резки – плавлением и испарением. Однако последний механизм требует высоких энергозатрат и осуществим лишь для достаточно тонкого металла. Поэтому на практике резку выполняют плавлением. При этом в целях существенного сокращения затрат энергии, повышения толщины обрабатываемого металла и скорости разрезания применяется вспомогательный газ, вдуваемый в зону реза для удаления продуктов разрушения металла. Обычно в качестве вспомогательного газа используется кислород, воздух, инертный газ или азот. Такая резка называется газолазерной.
Схема лазерной резки металла
Рисунок. Схема лазерной резки
Например, кислород при газолазерной резке выполняет тройную функцию:
вначале содействует предварительному окислению металла и снижает его способность отражать лазерное излучение;
затем металл воспламеняется и горит в струе кислорода, в результате выделяется дополнительная теплота, усиливающая действие лазерного излучения;
кислородная струя сдувает и уносит из области резки расплавленный металл и продукты его сгорания, обеспечивая одновременный приток газа непосредственно к фронту реакции горения.
В зависимости от свойств разрезаемого металла применяются два механизма газолазерной резки. При первом значительный вклад в общий тепловой баланс вносит теплота реакции горения металла. Такой механизм резки обычно используется для материалов, подверженных воспламенению и горению ниже точки плавления и образующих жидкотекучие оксиды. Примерами могут служить низкоуглеродистая сталь и титан.
При втором механизме резки материал не горит, а плавится, и струя газа удаляет жидкий металл из области реза. Данный механизм применяется для металлов и сплавов с низким тепловым эффектом реакции горения, а также для тех, у которых при взаимодействии с кислородом образуются тугоплавкие оксиды. Например, легированные и высокоуглеродистые стали, алюминий, медь и др.
Схемы подачи вспомогательного газа в зону лазерной резки
Рисунок. Схемы подачи вспомогательного газа в зону резки
Типы лазеров
Лазер, как правило, состоит из трех основных узлов:
источника энергии (механизма или системы накачки);
активного (рабочего) тела, которое подвергается «накачке», что приводит к его вынужденному излучению;
оптического резонатора (системы зеркал), обеспечивающего усиление вынужденного излучения активного тела.
Для резки обычно применяются следующие типы лазеров:
твердотельные и
газовые – с продольной либо поперечной прокачкой газа, щелевые, а также газодинамические.
В осветительной камере твердотельного лазера размещаются лампа накачки и активное тело, представляющее собой стержень из рубина, неодимового стекла (Nd-Glass) или алюмо-иттриевого граната, легированного иттербием (Yb-YAG) либо неодимом (Nd-YAG). Лампа накачки создает мощные световые вспышки для возбуждения атомов активного тела. По торцам стержня расположены зеркала – частично прозрачное (полупрозрачное) и отражающее. Лазерный луч усиливается в результате многократных отражений внутри активного тела и выходит через частично прозрачное зеркало.
Длина волны излучения углекислотных лазеров составляет 9,4 или 10,6 мкм.
Твердотельные лазеры плохо обрабатывают неметаллы, поскольку ряд таких материалов полностью или частично прозрачен для излучения с длиной волны около 1 мкм, например, оргстекло. Лазерный луч более чувствителен к неровной поверхности обрабатываемого материала. Однако при раскрое алюминиевых сплавов, меди и латуни твердотельные лазеры имеют преимущество по сравнению с углекислотными, поскольку поглощение излучения поверхностью этих металлов значительно выше на длине волны твердотельного лазера.
Углекислотные лазеры более универсальны и применяются для обработки почти любых металлов и неметаллов. Кроме того, у них очень низкая расходимость луча, что дает возможность разместить источник излучения далеко от зоны обработки без потери качества луча.
Резка различных материалов
Для разрезания металлов в основном требуется мощность лазера от 450–500 Вт и выше, для цветных металлов – от 1кВт и выше.
Резку углеродистых сталей чаще всего выполняют с применением кислорода в качестве вспомогательного газа. В результате взаимодействия кислорода с нагретым лучом металлом протекает экзотермическая реакция окисления железа обычно с выделением в 3–5 больше тепла, чем от самого лазерного излучения. Качество торцевой поверхности реза – высокое. На нижней кромке реза характерно образование незначительного грата.
Наибольшую проблему представляет возможность перехода процесса резки, выполняемого на очень малых скоростях (как правило, менее 0,5 м/мин), в неуправляемый автогенный режим, при котором металл начинает разогреваться до температуры горения за пределами воздействия луча, что приводит к повышению ширины реза и увеличению его шероховатости.
В ряде случаев, например, при вырезке деталей с острыми углами и отверстиями малого диаметра, вместо кислорода предпочтительно использование инертного газа при высоком давлении.
Лазерная резка нержавеющей стали, в особенности больших толщин, затруднена процессом зашлаковывания реза из-за присутствия в металле легирующих элементов, влияющих на температуру плавления металла и его оксидов. Так, возможно образование тугоплавких оксидов, препятствующих подводу лазерного излучения к обрабатываемому материалу. Усложняет процесс резки и низкая жидкотекучесть раплавленных оксидов, например, свойственная для нержавеющих хромоникелевых и высокохромистых сталей.
Для получения качественного реза используется азот высокой чистоты, подаваемый при повышенном давлении (обычно до 20 атм). При резке нержавеющей стали большой толщины требуется заглубление фокального пятна луча в разрезаемый металл. Как следствие, повышается диаметр входного отверстия и возрастает подача газа внутрь металла в зону расплава.
Для лазерной резки алюминия и его сплавов, меди и латуни требуется излучение более высокой мощности, что обусловлено следующими факторами:
низкой поглощательной способностью этих металлов по отношению к лазерному излучению, особенно с длиной волны 10,6 мкм углекислотного лазера, в связи с чем твердотельные лазеры более предпочтительны;
высокой теплопроводностью этих материалов.
Обработка малых толщин может выполняться в импульсном режиме работы лазера, что позволяет уменьшить зону термического воздействия, а больших толщин – в микроплазменном режиме. Плазмообразующими являются пары легко ионизируемых металлов – магния, цинка и др. Под действием лазерного луча в области реза образуется плазма, нагревающая металл до температуры плавления и плавящая его.
При разрезании алюминия применяется вспомогательный газ с давлением более 10 атм. Структура торцевой поверхности реза – пористая с легко удаляемым гратом на нижней кромке реза. С повышением толщины металла качество торцевой поверхности реза ухудшается.
При резке латуни торцевая поверхность реза обладает пористой шероховатой структурой с легко удаляемым гратом в нижней части реза. С возрастанием толщины металла качество торцевой поверхности реза ухудшается.
Таблица. Характерные толщины разрезаемых листов при мощности лазера P = 5 кВт
Наименование Толщина (мм)
Углеродистые и легированные стали до 40
Нержавеющая сталь 25
Медь 5
Латунь 12
Сплавы алюминия 12
С помощью углекислотных лазеров возможна обработка различных неметаллов – фанеры, дерева, ДВП, ДСП, пластика, оргстекла, полиэфирного и акрилового стекла, ламината, линолеума, резины, ткани, кожи, асбеста, картона и других.
Установка лазерной резки по причине загорания невозможна или очень затруднена резка толстого пенокартона (при толщине более 10 мм).
Невозможен или крайне сложен раскрой лазером таких материалов как текстолит, стеклотекстолит, гетинакс, сотовый полипропилен, поликарбонат, сотовый поликарбонат. Затруднено разрезание материалов, склонных к растрескиванию, например, керамики или стекла.
Таблица. Характерные толщины разрезаемых листов при мощности лазера P = 1,5 кВт
Наименование Толщина (мм) Скорость резки (м/мин)
Пластмасса 25 2
Фанера 10 3–4,5
Высушенная сосна 20 2
ДСП 20 1,5
ДВП 5 6
Стекло 1–8 5–0,5
Асбест, металлоасбест, паронит 4 1,5
Технологические параметры
Основными технологическими параметрами процесса лазерной резки являются:
мощность излучения;
скорость резки;
давление вспомогательного газа;
диаметр сфокусированного пятна и др.
При импульсном режиме к данным параметрам добавляются:
частота повторения импульсов;
длительность импульсов;
средняя мощность излучения.
Эти параметры влияют на ширину реза, качество резки, зону термического влияния и другие характеристики.
Это интересно:
Симоронский ритуал "мобильник желаний"

Показать еще...
Лучший выбор при ремонте потолков

Кэмри удачная модель от Тойота
Опытным автолюбителям известно, что модельный ряд Тойота Камри является одним из самых востребованных и популярных на рынке Восточной Европы.Магия для бизнеса и работы

Тайные силы родного дома

Как правильно подобрать украшения


Комментарии
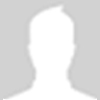
Комментарии: 0